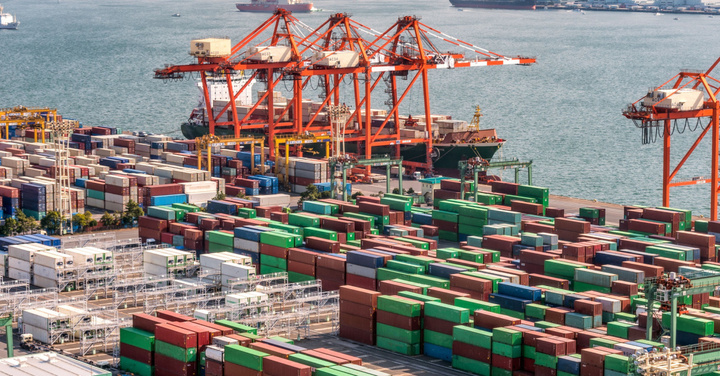
Drayage shipping plays a pivotal role in supply chain logistics, ensuring containers are taken from the port and sent to the proper location on time. The drayage journey is often short, but without this crucial aspect of the transportation process, goods may be left at the port or ramp too long, meaning delays and fees. With the global e-commerce boom, customers want products delivered as quickly as possible, and drayage helps the supply chain run more efficiently.
A proper drayage system is a well-oiled machine, while an improper one suffers breakdowns and a disruption in the flow of goods, a loss of money, and poor customer service. This article will discuss how drayage trucks can make your business run smoothly, how to overcome faulty systems that cost time and money, and how Port X Logistics can help optimize your drayage process.
The Benefits of Drayage Systems
Drayage freight services play an essential role in the transportation network and can help bridge the gap across shorter distances in the supply chain. Here’s how delivering the containers to an intermediary can help:
- Cost savings – Proper drayage means a reduction in overall transportation costs. Fewer staffing hours are required to run a properly functioning drayage system, saving labor costs. There are reductions in fuel and storage costs, with a decreased risk of shipment damage. Drayage trucks provide an affordable way to recover and transport goods while optimizing delivery schedules.
- Time savings – Drayage means wait times at the ports and hubs are reduced, with quicker shipment turnaround times. There may be fewer delays due to unexpected problems and reduced time spent on paperwork and processing. The shorter haul means fast delivery times, as the shipment usually travels within the same town or city. This ensures a more efficient process of moving goods to the proper destination.
- Improved efficiency – Shorter delivery times increase productivity and lessen the time spent waiting on delivery. Moving full and empty containers to the appropriate places to clear space helps streamline the entire supply chain process. Adequate planning means there will be enough space in warehouses and distribution centers.
- Accuracy – Cloud-based services and mobile apps help ensure that each shipment is delivered to the right place at the right time. Stakeholders always know each shipment’s status, thanks to real-time visibility and collaboration offered by Turvo. This insight reduces the risk of a load going to the wrong destination or not being delivered in full. Reliable models and forecasts ensure accuracy.
- Security – An experienced drayage system team knows all regulations and how to keep cargo secure, complete, and intact while in transit. Businesses won’t need to worry about damaged goods. Containers are moved out quicker and are not just sitting unattended at the port or ramp for long periods.
The Impact of Poor Drayage Services
A substandard drayage process puts a company in a challenging spot. Here are ways a business suffers if it has a poor, inefficient drayage service in place:
- Shipment visibility – Without real-time tracking and monitoring, not all parties know where the cargo is, leading to confusion and distrust. Time-sensitive goods may miss the scheduled delivery time if visibility isn’t available throughout the process.
- Customs clearance – Clearing customs often results in long delays that put the supply chain process behind schedule. Delays mean late shipments and increases in costs that can result in poor customer service. Moving across borders is a complicated process, made even worse if proper documentation isn’t handy. Companies that need help with having all their ducks in a row lose valuable time here.
- Increased detention and demurrage costs – Detention and demurrage fees add up quickly if containers aren’t moved on schedule by the end of their free time. If the drayage process is too slow, the delay costs money, slows down the supply chain, and puts everyone behind schedule.
- Delays for reshuffling – Reshuffling containers can be time-consuming as they must be moved and repositioned. An efficient team turns reshuffling into a benefit, reducing the trucks needed and lowering transportation costs. But inefficient teams are delayed in this process.
- Delays in delivery and receiving of goods – Inefficient drayage services lead to the product arriving late to its next destination. There may have been inaccuracies in capacity planning, and an insufficient number of trucks are available. Delays lead to customer dissatisfaction and damage the company’s bottom line.
- Increased costs – Fees are enforced if shipments aren’t moved in the proper timespan. There may be added expenses in fuel costs, labor costs, and even processing paperwork if there is too much inefficiency. Poor route selection also may result in increased costs.
- Safety issues – Inferior drayage services lead to problems like inadequate loading and unbalanced, unsafe cargo. Improper vehicle maintenance may result in accidents.
- Damaged goods – Without the right team, improper handling and loading may result in part or all of the shipment being ruined. The risk of damage to the goods will be high if proper precautions aren’t taken.
- Low quality of service – All of the above issues can result in having the shipment put way behind schedule or even ruined. The consequence of too many of these issues is customer dissatisfaction and a ruined reputation. With the boom in e-commerce, poor service quality leads customers to seek alternatives.
Drivers of Poor Drayage Services
The problems above stem from three encompassing areas that must be tackled before drayage service can improve and run smoother:
- Lack of expertise – An employee shortage continues to impact the transportation industry, resulting in a loss of talent and experience. More time and money are needed to bring new employees up to code. The lack of proper expertise leads to an abundance of problems and inefficiency all along the supply chain. The loss of time and money is much more noticeable in replacing experienced workers with inexperienced ones.
- Poor communication – A lack of technology results in poor communication among all parties, as critical data remains siloed. Without visibility, stakeholders are unaware of what others are doing, resulting in delays and incorrect information sharing. Without real-time monitoring, there is a much higher risk of a lost shipment or not having merchandise picked up promptly. Poor communication can result in customer service issues, as all the confusion hurts the bottom line.
- Unclear instructions – Confusion regarding deliveries slows down the process. Running the wrong routes or not having the proper paperwork ready when needed increases the risk of delays, added costs, and wasted time. Customers may even be the reason for the issue if they are unclear about their needs.
Tips for Improving Drayage Efficiency
Problems in the drayage system can be fixed. Automating the process may be the quickest solution, allowing real-time visibility that monitors the tracking process at all times. Data analytics help the company understand the end-to-end process and where fixes are needed. Receiving real-time notifications and alerts helps prevent logjams that tie up employees.
Some ports have been slow to advance technologically, so planning and forecasting are necessary to deal with this issue. A plan is needed for faster container deconsolidation to get the products on their way more efficiently. Proper storage at warehouses means goods aren’t left stranded at the port, which avoids fees and protects from loss or theft.
Keeping drivers and other employees content can also help future success. Allowing drivers to set their schedules may mean they want to keep working for you. Letting drivers perform dual transactions keeps them moving more efficiently and reduces wasted time. Retaining talented employees happy means they’ll stay. There won’t be the hassle of having to hire and train new employees over and over.
Port X Logistics Can Streamline Your Drayage System
An improperly run drayage system results in numerous issues that can crush a company. Too many delays and inefficiency cause problems throughout the supply chain, costing money in fees and losing customers. Drayage is usually a short part of the transportation process but is also one of the most important. Not focusing on it enough can spell doom.
There are drayage solutions available. A company like Port X Logistics uses drayage efficiency to eliminate unnecessary costs while passing the savings on to customers.
Working with Port X Logistics allows you to turn drayage into a positive for your company. Its experts move with urgency and move your containers from all ports and ramps in the United States and Canada while tracking your shipment from start to finish along the supply chain process – providing clear communication the entire way. Port X Logistics has experience tackling drayage obstacles and quickly adapts to each issue that arises. It tracks containers from the origin to the final delivery with complete visibility, cutting down on communication difficulties. Visit the Port X Logistics website to work with them and improve your drayage system.