Port of Houston
1916 words 8 minute read – Let’s do this!
As Memorial Day approaches, the team at Port X Logistics pauses to honor the courage and sacrifice of the U.S. service members who gave their lives for our freedom. In an industry that thrives on movement, we reflect on the heroes who made it possible for us to live, work, and ship in peace. While operations slow this weekend in remembrance, the freight keeps flowing — and we’re here to keep you informed and prepared. Don’t forget to follow our LinkedIn page to see other company news and industry related topics and to get on the list for this weekly Market Update Newsletter and future industry related news sent directly to your inbox email marketing@portxlogistics.com.
Following last week’s temporary tariff reduction from 145% to 30%, there has been a substantial uptick in cargo bookings from China to the U.S. Reports indicate a 275% week-over-week increase in shipping bookings, as importers rush to capitalize on the temporary relief. Major U.S. retailers including Walmart, and several clothing brands are racing to secure China-made merchandise for the busy summer shopping season starting in late May after Washington and Beijing agreed to temporarily slash tariffs. This surge mirrors the post-lockdown shipping boom of 2020, potentially leading to similar challenges such as port congestion and increased freight rates. Understanding past disruptions can help businesses better prepare for and navigate the complexities of the current shipping landscape.
The 90-day pause has stirred movement across major ports, especially in Los Angeles, but it hasn’t settled the broader tension. While cargo volumes are climbing and retailers are rushing to restock, the structural problems in global trade—particularly the U.S. trade deficit—remain untouched. Since the tariff relief went into effect, ocean freight bookings from China to the U.S. jumped by 275%. That’s not a subtle shift—it’s a sharp reaction from American importers trying to get ahead of any future disruption. Big-box chains and wholesalers are scrambling to secure inventory, not because they expect a lasting resolution, but because they don’t trust that one is coming. At the Port of Los Angeles, shipping activity has picked up rapidly. Port officials noted an influx of high-volume shipments, especially consumer electronics, home goods, and food-related imports. There’s a clear push to rebuild inventory for summer and fall retail seasons—yet the timeline is tight. Before the pause, Container bookings from China to the U.S. fell nearly 50% in the last week of April, according to data provided to brokerage TD Cowen by container tracking firm Vizion. Several U.S. companies paused orders when President Trump hit Beijing with retaliatory and fentanyl tariffs on April 9th. U.S. businesses largely rely on ocean shipping but that can take between 30 and 60 days for goods to reach the United States from China, depending on the destination and ship size. U.S. retailers and apparel companies typically begin shipping merchandise from China at least two to three months before the summer season starts on Memorial Day.
The pause may have eased the surface-level friction, but it hasn’t done anything to fix the core issue: the U.S. continues to import far more than it exports. The current account deficit remains wide. Even with tariffs temporarily reduced, the imbalance is structural, not seasonal. Instead of addressing the root causes, Washington has leaned on stimulus-style policies and tax incentives. Treasury data suggests the federal deficit could rise to 7–8% of GDP over the next ten years without offsetting measures. Meanwhile, Beijing has held back on opening its markets up in meaningful ways, maintaining tight control over key sectors.
If you’re in manufacturing, retail, or food service – especially sectors relying on imported materials like spices, packaging, or electronics. This pause may feel like a breather. But don’t mistake it for stability.
Inventory risk is high: Short-term availability is improving, but future pricing remains unpredictable.
Shipping capacity is tight: With everyone trying to move product at once, freight delays are likely.
Policy shifts are not over: The U.S. government has signaled it may reintroduce steep tariffs if trading partners are deemed “non-cooperative.”
While the headlines focus on steel and semiconductors, specialty imports like spices are quietly absorbing the pressure. Many spice blends or single-origin ingredients come through China or pass through ports affected by these policies. Even a brief disruption in freight movement or customs processing can impact availability and costs.
This tariff pause is just that—a pause. It’s not a new agreement or a reset. It’s a temporary measure, and businesses should plan accordingly.
Talk to your suppliers now about Q3 and Q4 needs.
Watch for July updates—the 90-day window closes in August.
Diversified sourcing Let Port X Logistics help lead the way!
U.S. Importers are now preparing for a surge in cargo that could lead to higher shipping rates and consumer costs. Uncertainty means higher costs – Shipping rates are already rising. The World Container Index from supply chain firm Drewry showed that rates for the week ending May 15th were up 8% from the prior week. The report also showed that rates for freight shipping from Shanghai to New York jumped by 19% and rates from Shanghai to Los Angeles increased by 16%. The increase is a rebound for volumes that dipped at the beginning of the month as the 145% tariff on Chinese goods slowed demand. Despite the rush to deliver goods to the U.S., freight rates have not yet spiked. The spot rate to send a 40-foot container from China to the U.S. West Coast rose 3% week-on-week to $2,395 on May 19th, data from freight booking and payments platform Freightos shows, indicating that businesses were not swamping shippers with bookings.
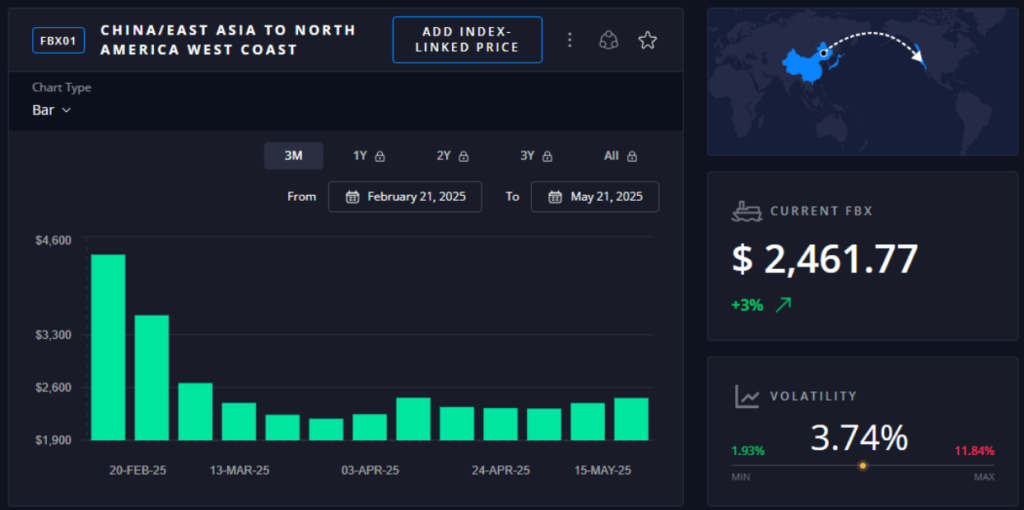
Import TEUs are up 6.8% this week from last week – with the highest volumes coming into Los Angeles 18.4%, Long Beach 15.5% and Newark 16%. The key tariff pause issues we talked about previously in the Market Update have led to extended dwell times, with containers remaining in terminals longer than anticipated, thereby exacerbating congestion. See below for how it is currently affecting the LA and LGB ports.
What’s happening at the ports and rails?
You can find all the information on the below link where we cover port congestion, chassis issues and capacity lead times weekly at all U.S. and Canada Ports and rail heads on our website – click on the link below
LA/LGB: The average on-dock rail dwell time at the Los Angeles Port has increased to approximately 4.9 days, surpassing the optimal range of 2–4 days. Local import dwell times at the Port of Long Beach range between 4 to 8 days, indicating congestion within terminal operations. These extended dwell times are attributed to a significant increase in cargo volumes as importers expedite shipments to take advantage of the 90-day tariff suspension.
Contributing Factors:
- Surge in Imports: The temporary reduction in tariffs has led to a substantial uptick in cargo bookings from China to the U.S., putting pressure on port infrastructure.
- Rail Car Shortages: There is a reported shortage of rail cars available to move the increased volume of containers, leading to delays in transporting goods inland.
- Terminal Congestion: The accumulation of containers awaiting rail transport is causing congestion at the terminals, further exacerbating delays.
Should You Reroute Freight Inland? Given the potential of increasing congestion, you might consider alternative strategies – Transloading cargo to domestic trailers for inland trucking can bypass rail delays. Our Los Angeles drayage yard and transload warehouse location boasts a large drayage fleet, a large, secured yard with plenty of yard storage space and a transload warehouse with immediate capacity to pull your containers for palletized and floor to pallet transloads. Our capacity is tendered to on a first come first serve basis – We ALSO have access to OpenTrack and can track your containers from the moment they get loaded to the overseas vessel all the way to the U.S. port of arrival. And let’s not forget: We offer a NO DEMURRAGE GUARANTEE on all orders that have been dispatched to us 72 hours prior vessel arrival and are cleared for pickup by the last free day. Don’t let all our capacity slip through your fingers, front loading volumes, vessel backups and rail dwells will make LA transloads the hot commodity, contact the team to get on the capacity list, for rates and any questions letsgetrolling@portxlogistics.com
Houston: New Reefer Import Dwell Fees Effective July 1st . To enhance terminal efficiency, Port Houston will implement new fees for refrigerated (reefer) import containers that exceed free time allowances, effective July 1, 2025. These charges apply after the expiration of free time, including days when terminal truck gates are closed due to scheduled closures.
The fees are structured as follows:
1–3 gate days: $51.60 per day
4–7 gate days: $77.40 per day
8–13 gate days: $103.20 per day
14+ gate days: $154.80 per day
Port X Logistics has drayage assets in Houston with the capability of long-haul drayage and we have a transload warehouse in LaPorte that can transload anything from standard pallets, to heavy lumber and industrial coils. If you need help in the Houston area we got your back, we also have a drayage network with trucks and yard space servicing the Dallas area contact letsgetrolling@portxlogistics.com
Denver: Union Pacific plans to continue operating trains and most intermodal terminals during the Memorial Day holiday – However, due to light volumes, there may be train consolidations and/or annulments, potentially causing slight delays in shipment availability. Interline shipments might also experience some delay if connecting railroads reduce operations for the holiday. If you are looking for drayage services into and out of the Denver ramps, our Denver operation is in the heart of the transportation district @ I-25 and I-70 in Denver, Colorado, located within four miles of both the UP and BNSF Irondale ramps ensuring prompt and affordable service. With 12 trucks and growing, two acres of secure and monitored yard storage, AND a 25,000 sq. ft. transload warehouse and dry vans, we can help with a variety of your transportation, cross dock and storage needs. Contact the Denver team today for great rates and capacity letsgetrolling@portxlogistics.com
Did you know? We are equipped to make your holiday airfreight shipments run smoothly with minimal monitoring on your end? Our Carrier911 team consists of crisis management experts who have extensive experience in airfreight logistics. We stand ready 24/7/365 to handle your needs for Aircraft on Ground (AOG) Recovery, Hotshot Trucking, Expedited Transportation, Aerospace, Industrial & Automotive Logistics, Front & Back-End Charter Services, and First and Last Mile On-Board carrier (OBC) – Perfect for your upcoming urgent holiday weekend shipments. Our exclusive-use Sprinters, Straight Trucks, and Dry Vans are ready to meet your needs at a moment’s notice, 24/7, 365 days a year. We recognize that freight emergencies can happen at any time, and our dedicated fleet ensures we can respond swiftly. With Carrier 911, you can relax knowing you have real-time visibility of the driver’s location, day or night. The Proof of Delivery (POD) will also appear in your inbox immediately, guaranteeing timely receipt of your essential documents. For a free demo email info@carrier911.com or click the link below to schedule:
https://portxlogistics.com/tech-demo/
SONAR Import Data Images
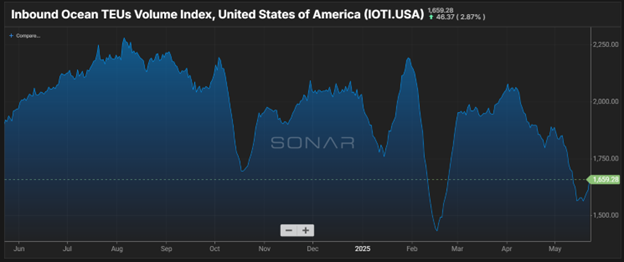
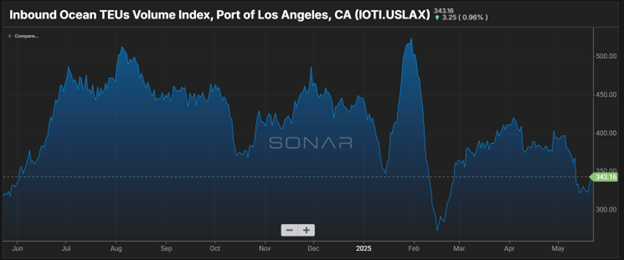
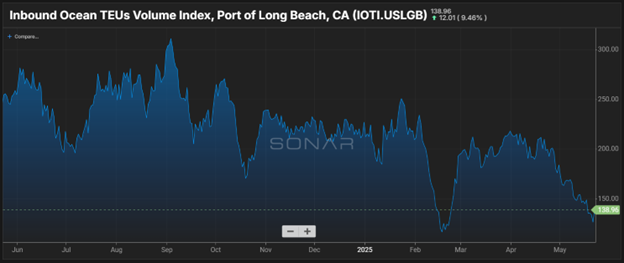
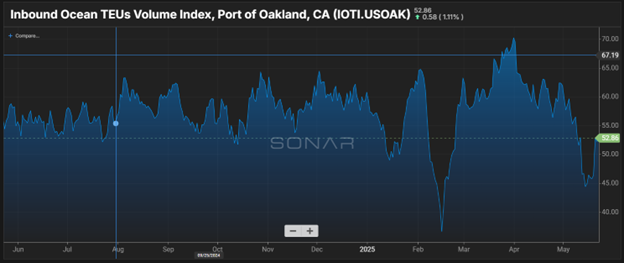
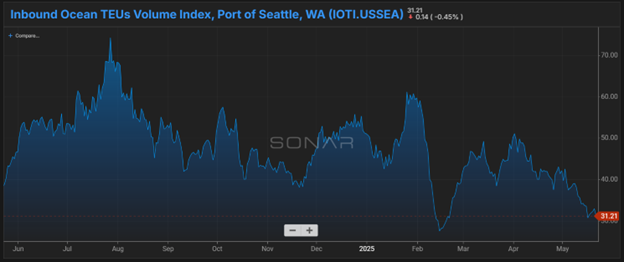
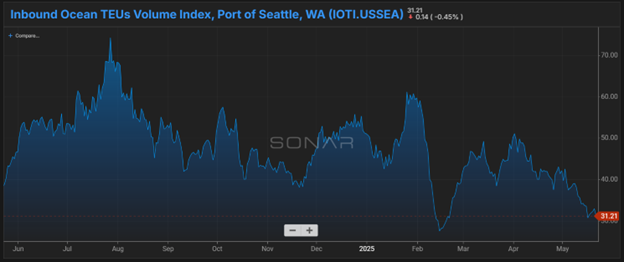
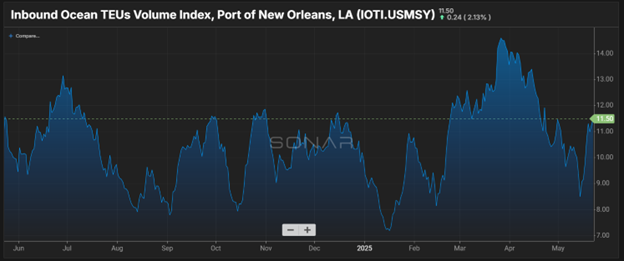
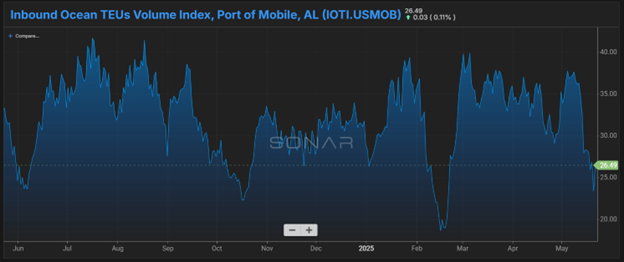
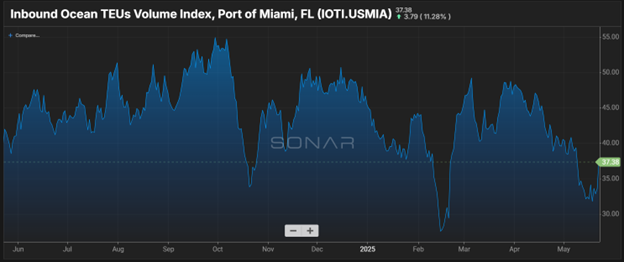
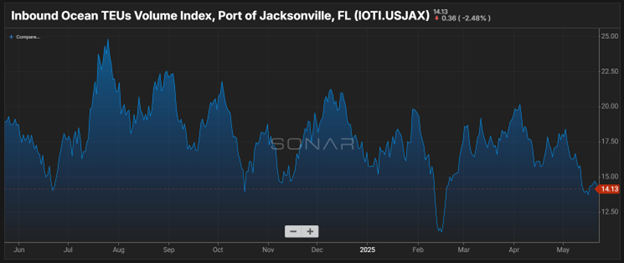
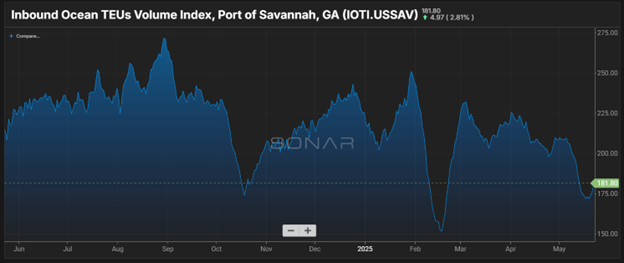
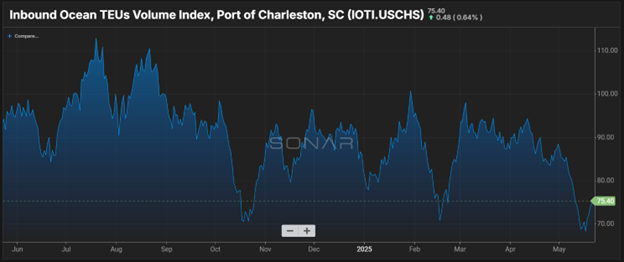
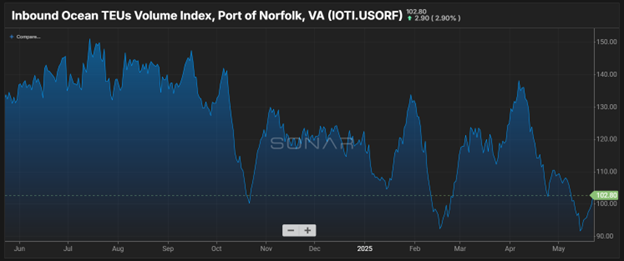
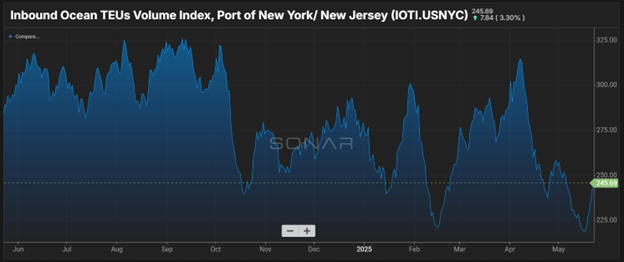
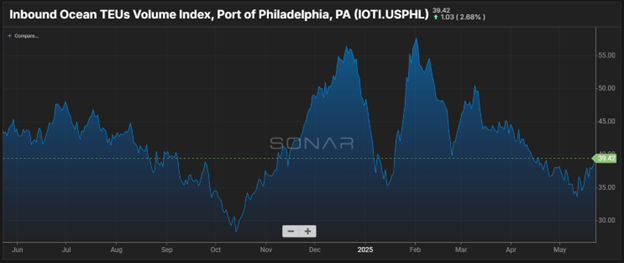
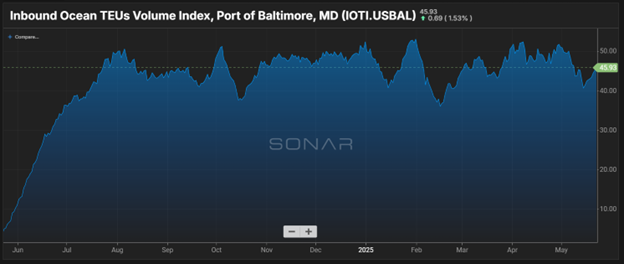
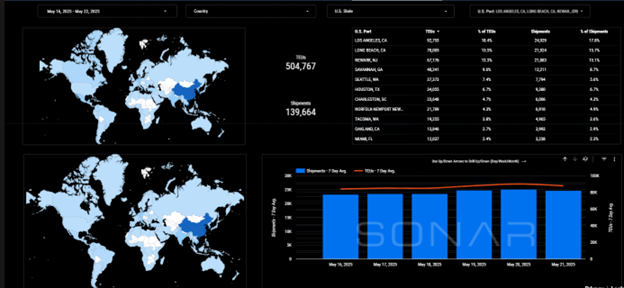
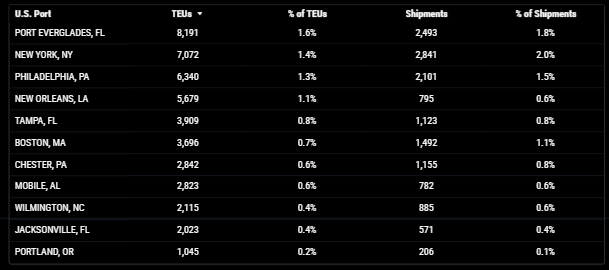
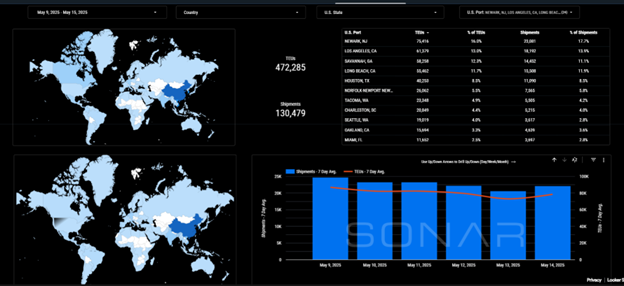
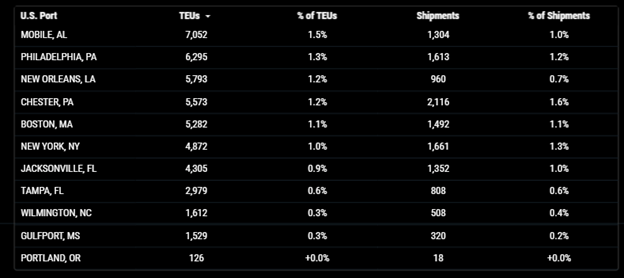