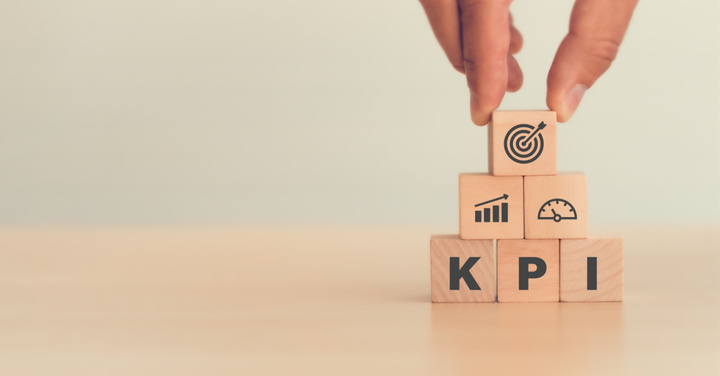
Evaluating logistics efficiency is a complex, tedious, and absolutely necessary component of business optimization. In today’s unpredictable and tumultuous freight market, assessing logistics and transportation functions is more critical than ever – but knowing what data to track can be overwhelming. Key performance indicators (KPIs) provide valuable insight into the inventory, transportation, and distribution processes that drive logistics efficiency.
This blog presents the foundations of logistics KPIs, how companies should approach KPI development, and a comprehensive list of essential logistics metrics.
Logistics KPIs: What are They?
Key performance indicators (KPIs) are data metrics that compare a company or department’s performance against internal goals or industry benchmarks. KPIs provide analytic value to help identify specific areas for improvement and guide more efficient, cost-effective decision-making. This is especially important for complex and multi-faceted logistics processes.
Logistics KPIs are quantitative tools companies use to measure performance within their logistics department. These typically include a variety of metrics to evaluate purchasing, warehousing, transportation, and delivery functions, with the aim of capturing data on both process and financial efficiency.
Why are Logistics KPIs Important?
Logistics teams are tasked with procuring the right amount of resources at the right time, transporting them to the correct location in good condition, and delivering them on time to the right customer. Any hiccup in logistics processes can have compounding impacts downstream and devastating financial consequences. Consistently measuring and monitoring logistics KPIs allows logistics teams to identify negative trends, proactively address issues, and improve overall operations.
Selecting the Right Logistics KPIs
Logistics encompasses a wide range of activities, including purchasing, warehousing, transportation, and distribution, with an even more comprehensive range of possible KPIs to evaluate performance at each level. Determining the right KPIs for a company’s unique logistics needs requires careful consideration and several steps.
Step 1: Define short- and long-term logistics goals.
These goals should help to solve current issues or optimize future processes. Some questions to consider when defining goals and selecting logistics metrics might include:
- How often are customer orders delayed due to backorders?
- How often is an order delivered late or in damaged condition?
- How much does it cost to deliver an order?
- What additional costs do transportation carriers charge?
- Why are overall labor costs increasing?
Step 2: Compare leading and lagging KPIs.
Different types of KPIs provide unique insights into a company’s performance, so understanding that difference is critical for KPI development.
- Leading KPIs measure performance before a process change is implemented and are used to predict changes or trends. Leading KPIs are forward-looking and indicate what a company is likely to achieve.
- Lagging KPIs measure performance after a process change and are used to form long-term trends. Lagging KPIs measure what was already achieved and help determine how well a process was managed.
In other words, a leading KPI informs a company of how to produce desired results, while a lagging indicator measures current performance outcomes. Finding a balance between leading and lagging KPIs creates a comprehensive view of logistics performance and guides thoughtful decision-making.
Step 3: Be SMART.
Ensure that KPI targets are specific, measurable, attainable, relevant, and time-bound. Lean on industry-standard benchmarks and internal historical data to ensure KPI goals are within reach. Additionally, be realistic about the number of KPIs included in a program. Managing logistics metrics can be time-consuming, so work within the company’s available labor resources and utilize existing data sources whenever possible.
Step 4: Create a team.
Collecting and analyzing KPIs shouldn’t be a solitary full-time job. Establishing a collaborative team that includes well-versed members from each stage of the logistics process ensures that all relevant KPI data is being considered and collected to drive improvements and reach goals.
Step 5: Review and revise KPIs.
Regularly review KPIs, as well as the internal and external factors that contribute to the metrics. Understanding what components your logistics team can control, and also what they cannot, should drive decision-making and help determine when to add or remove specific metrics from the KPI program.
With these tips for KPI selection in mind, let’s look at the most essential and critical metrics at each stage of the logistics process.
The Essential Logistics KPIs
Move these to the top spot: Port X Logistics/Carrier911 — Draft: The Ultimate Guide to Logistics KPIs
However, let’s also make sure we state WHY these are first (Because PXL is good at it!)
Supply & Inventory KPIs
Supply and inventory metrics measure the effectiveness of purchasing and production processes and how well final goods move through the distribution process. These KPIs provide valuable insight into receiving operations and inventory management within the logistics chain.
- Receiving Efficiency: Measures the time between when a warehouse receives an incoming PO and when those items are ready for sale. This should include new stock as well as returns, and account for the time taken to confirm counts and stock shelves.
- Capacity Utilization: Measures how much of a resource a company is using. Every company has a maximum capacity for manufacturing and production. Logistics managers can better manage production rates and lower operating costs by monitoring capacity utilization — calculated by dividing actual production rates by the maximum production rates.
- Pick and Pack Cycle Time: The amount of time it takes a warehouse employee to pick a product off the shelf and pack it. Tracking this KPI can help identify inefficiencies in the product line.
- Inventory Accuracy: Metric to establish whether inventory counts recorded in an inventory management system reflects the actual physical inventory count. Calculate this by dividing the database inventory count by the physical inventory count. This metric is vital for preventing stockouts and backorders.
- Inventory Turnover: Also known as stock rotation, this measures how many times a company sells all inventory of a particular item in a given period. High inventory turnover suggests a strong sales strategy, high demand for goods, and accurate inventory forecasting.
- Inventory to Sales Ratio: This metric evaluates the amount of available product in inventory compared to the actual number of sales. Overstocked inventory is often a significant expense, so companies that can keep inventory expenses closely matched to sales also keep valuable capital in hand.
- Customer Backorder Rate: Measures how often a company cannot fulfill a scheduled order due to out-of-stock inventory. This metric directly contributes to customer satisfaction and negatively affects repeat orders and brand loyalty.
- Number of Shipments: How many shipments a company sends out in a given period. Over time this KPI identifies trends and patterns, helping logistics teams plan resource and labor allocation to maximize efficiencies and minimize costs.
- Productivity: A measure of how efficiently machines, departments, or people operate. Measuring and understanding productivity ensures that a company has the resources they need to meet customer demand.
Order Fulfillment KPIs
Order management is critical to the customer experience. Fulfillment metrics measure efficiencies in order processing and can identify issues that lead to poor customer satisfaction and costly returns.
- Lead Time: Also known as order cycle time, this KPI measures the amount of time between when a customer places an order and when they receive it. This metric is vital for identifying bottlenecks in the fulfillment process.
- On-Time Shipping: A vital metric for customer satisfaction, this measures the percentage of orders shipped on or before the requested date.
- On-Time In-Full: A critical customer-focused delivery metric, this represents the percentage of shipments delivered according to the quantity and schedule requested when the order is placed. Did the customer get what they ordered when they wanted it?
- Order Picking Accuracy: The ratio of error-free orders over the total orders shipped. This metric is critical for monitoring warehouse efficiency and minimizing costly returns due to customers receiving the wrong product.
- Rate of Return: The percentage of returned orders in relation to total fulfilled orders. Almost one in three online orders get returned, so tracking return rates and the reason(s) for them is essential for improving fulfillment processes and customer satisfaction.
- Shipping Cost per Order: Calculate this fulfillment performance metric by dividing the total shipping costs over a certain period by the total number of successful deliveries in the same period. Shipping costs can erode margins, so closely tracking them is critical for protecting profits.
Transportation KPIs
Whether managed by an in-house fleet or outsourced to external carriers, transportation plays a major role in logistics. Metrics that capture transportation performance and costs are critical for logistics optimization.
- Trailer Utilization Rate: Measures how efficiently companies load their trailers to maximize available space. This rate reflects a company’s load planning and can identify opportunities to consolidate or utilize other modes of transportation.
- Truck Turnaround Rate: Also known as truck turning, this KPI measures the time a truck enters a warehouse to collect or deliver products to when it exits the facility. This metric reflects loading and unloading efficiency and should be kept low to optimize driver hours.
- Average Wait Time: Similar to truck turnaround, this measures the time a truck waits to be loaded or unloaded and indicates how smoothly a facility is functioning. Lower wait times help keep drivers happy and minimize carrier detention fees.
- Delivery Time: Measures the time from when a shipment leaves the warehouse to the moment it is delivered to a customer. This metric is especially valuable in the last mile but can also help pinpoint bottlenecks in multimodal delivery models.
- Driver Performance: Often a combination of multiple KPIs that evaluate drivers’ efficiency and safety while on the road. This evaluation may include metrics on speed, idle time, hard-braking occurrences, and fuel usage to create a driver scorecard and identify areas for improvement. This metric is particularly important for monitoring driver safety practices and preventing dangerous and costly accidents.
- Fuel Efficiency: Measures the performance of vehicles on the road based on trends in mileage per gallon of fuel. This metric can help identify trucks that may require maintenance checks, low-performing drivers, or suboptimal route planning.
Drayage and Port KPIs
Drayage metrics are a subset of transportation KPIs and can provide unique insights into ocean freight and port process performance.
- Vessel Schedule Reliability: Measures the difference between the date a carrier advertises for a vessel to arrive at a port versus the date it actually arrives. This metric can be expressed as a percentage of on-time arrivals or as the average deviation (in days) between the expected arrival and actual arrival for a given vessel or carrier. This KPI helps logistics teams make better-informed decisions when weighing costs against schedule reliability, particularly for time-sensitive shipments.
- Vessel Discharge to Final Delivery Cycle Time: Departure times and delays at ports can be critical to identifying problems in loading and unloading. Vessel discharge times and final delivery times are vital for improving ocean and truckload freight processes.
- Demurrage & Per Diem Costs: Ocean freight costs can skyrocket when containers are not picked up and offloaded promptly. Demurrage fees apply to cargo while a loaded container is still at the port waiting to be picked up, while per diem fees apply to the carrier’s equipment held outside the port. Monitoring demurrage and per diem costs helps identify issues in the drayage process and is critical to managing transportation budgets.
- Average Inland Transit Times: A measure of ground freight carriers, this measures the time it takes to transport ocean cargo from its discharge port to its final destination or intermodal hub. This metric helps to evaluate drayage, trucking, and intermodal carrier efficiency and reliability — and helps guide carrier selection improvements.
- Container Turnaround Time: This metric captures similar information on how long containers sit at an importer’s warehouse between delivery and return. Measuring this helps identify and mitigate accruals that result from warehouse productivity or drayage partner return practices.
- Freight Awaiting Loading or Unloading: Monitoring load and unload times at departure and arrival ports provides vital information about supply chain performance and processes. These KPIs help streamline processes and identify areas in the transportation route that experience the most frequent delays.
Move Beyond Metrics with Port X Logistics
Logistics KPIs are the backbone of supply chain and transportation efficiency, but they mean nothing if they are only numbers in a report. Turning data-driven KPIs into action is essential for improving supply chain performance and delivering cost savings. The right freight partner can help importers analyze logistics KPIs and guide decision-making to enhance supply chain outcomes.
Port X Logistics can track cargo throughout the freight lifecycle, collect critical freight and logistics KPI data, and provide valuable analytic insights to improve logistics processes. Ready to learn more? Contact Port X Logistics today to discover their tracking, monitoring, and KPI solutions.