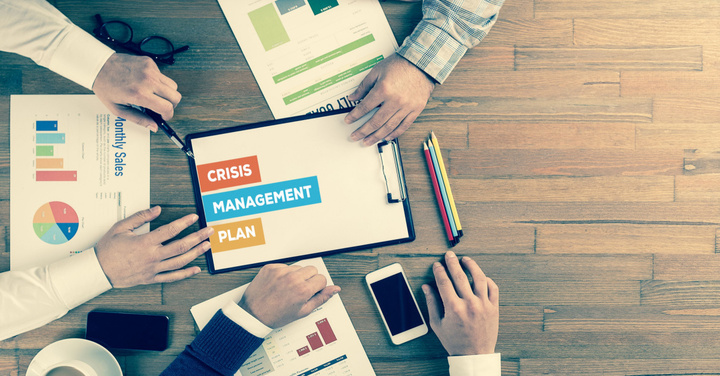
Every business runs into its share of challenges. Sometimes they are expected — employee turnover, a blip in order volumes, or price increases are a few examples. Other times, it is impossible to predict obstacles that occur. A supplier closes its doors, a weather event shuts down ports or transportation within a region, or a geopolitical event significantly impacts raw material supply or consumer demand.
When the latter takes place, it’s called a black swan event. These occurrences are so unusual that they cannot be forecasted — and can cause serious headaches for companies that move freight. But while it might be impossible to foresee a black swan event, shippers can still circumvent some of the problems they cause by partnering with the right providers and utilizing the right technologies.
Black Swan Events & How They Impact Freight Flows in the Supply Chain
A black swan event is defined as an event that cannot be anticipated. Former Wall Street trader Nassim Nicholas Taleb coined the phrase black swan event in his 2001 book, Fooled By Randomness. Black swan events can be positive or negative, but the adverse events are the ones that require more attention and planning. Some examples of black swan events include the 9/11 terrorst attacks on the World Trade Center and the 2008 financial meltdown. The COVID pandemic could also be classified as a black swan event.
Adverse black swan events blow a hole in lean supply chain management. In the past, companies would design their supply chains to be as cost-efficient as possible to reduce costs while meeting demand. Often this meant slashing inventory and reducing the number of suppliers in low-cost countries on the other side of the globe.
Lean supply chain management makes sense if there are no black swan events. Companies use lean management principles to eliminate waste and cut expenses while meeting ongoing customer needs.
The trouble is that black swan events are becoming less rare. In fact, author Yossi Sheffi argues that black swan events will only grow as time passes because the past is bounded, but the future is unbounded. As black swan events become more common and increase in magnitude, they will continue complicating inventory management and interrupt freight flows.
A need to inoculate supply chains against unpredictable adverse occurrences arises out of that predicament. Companies that invest in visibility solutions and partner with vendors that have a robust combination of technology and experience will be in the best position to manage the next black swan.
What Types of Black Swan Events May Cause a Crisis in Freight?
Black swan events can occur on a local level, or they may reverberate globally. Here are a few examples of black swan situations that could tangle a supply chain:
- An assembly line is on the verge of shutting down production because of part shortages. We saw this in the wake of the COVID pandemic. Factory shutdowns resulted in fewer parts being produced, including components needed by manufacturers to continue production.
- A major steamship line closing its doors with little warning. Remember Hanjin? In 2016, the world’s seventh-largest container shipping line declared bankruptcy and folded.
- A major thoroughfare is compromised. An example of this occurred in 2021, when the Ever Given ran aground, blocking commerce in the Suez Canal. The maritime journal Lloyd’s List estimated that the Ever Given held up $9.6 billion in freight each day that it was stuck.
- Port Closures. At the height of COVID, ports closed on both sides of the Pacific. In 2021, vessels had to be diverted from Ningbo thanks to coronavirus restrictions, spreading congestion to other Chinese ports. And ports across the United States saw record volumes for most of 2021, which slowed container processing.
- Inclement Weather. Hurricane Ian made headlines recently when it claimed the lives of hundreds of people in Florida and North Carolina. Outside of the human toll, the storm closed ports across Florida, Georgia, and South Carolina and reduced rail and trucking operations out of those states.
- Surges in Demand. While this could be an example of a positive black swan event, it is still difficult to manage. Consumer expenditures jumped 15.7% in the second quarter of 2021. It squeezed transportation capacity and sent rates climbing as suppliers attempted to keep up with demand.
Solutions for Crisis Management Spurred By a Black Swan Event
In the short term, companies must react to black swan events rapidly. For this to happen, they need access to data. Businesses must look at their entire end-to-end supply network, from raw material suppliers to end consumers. If an organization cannot identify its nodes, their size and value, and general fulfillment flow patterns, that company will be at a disadvantage.
Once a company has gotten visibility into its supply network, management can plan a response to different disruption scenarios. Take the port situation described above. If a port shutdown in another geographic location and excess cargo piles up at a company’s usual port, that business has to be prepared to adapt and respond accordingly.
Having visibility tools in place is crucial, but it is only a first step. Once shippers are familiar with their supply chains, they need to identify their greatest potential failure areas and devise a contingency plan to address those weaknesses. Is it a small pool of raw material suppliers? Or is manufacturing concentrated all in one location?
Another area of potential weakness is cargo recovery. In the current freight ecosystem, it’s easy for cargo to get lost or held up. But if a shipment is time or temperature sensitive, recovering it is urgent. Here are three solutions that can help.
- Accelerated Cargo Recovery – When a black swan event disrupts cargo operations, moving time-sensitive shipments out ASAP is essential. Port X Logistics’ sister company, Carrier911 offers expedited freight recovery services from any airfreight facility or container freight station in the United States. Most of the time, our team of experts will recover cargo in just one hour.
- Full Range of Expedited Capacity Options – Once a shipment arrives in the U.S., Port X Logistics can offer a range of services to retrieve it quickly. Port X Logistics meets emergency transportation needs with a dry van, a straight truck, or a sprinter equipped for immediate pickup.
- Pinpoint Instant Tracking – When there’s a freight emergency, retrieving cargo as quickly as possible is only part of the equation. Shippers also need to know where a shipment’s location at all times. Port X Logistics uses GPS and geofencing technology to provide real-time tracking capabilities because no one should have to wonder where their cargo is or when it will arrive.
The Role of Technology in Freight Crisis Management
Freight crisis management cannot happen without the right assortment of technology solutions. It’s critical that shippers and carriers have access to a shipment’s status and can communicate with one another easily. Technology should provide the following capabilities to shippers and their carrier vendors.
- Data – Organizations need access to data. They must be able to identify both supply and demand patterns and know what drives them to ward off emergency situations.
- Visibility – To expedite a shipment, carriers must know its location and status at all times. Especially with a black swan event, network visibility helps identify the choke points as they arise, not after they’ve happened. Through its Turvo driver app, Port X Logistics offers visibility into every step of an expedited shipment’s journey.
- Network Optimization – Carriers need a contingency plan to manage emergencies even before they happen. Freight tech should help carriers optimize their network to ensure they can always pick up cargo seamlessly.
- Collaborative Portal – Of course, emergencies will still arise regardless of how much planning takes place. When adversity strikes,all players must be able to communicate with each other. This might mean sharing a demand forecast or collaborating to improve plan accuracy.
Today’s supply chains are rife with potential pitfalls. Black swan events often immediately impact supply networks, followed by far-reaching ripple effects that sometimes continue for years. As discussed in this article, these events usually come out of nowhere.
Companies may not have a crystal ball, but they can develop contingency plans when a black swan event creates a freight emergency. One essential step is to work with a cargo recovery provider. Port X Logistics along with Carrier911, specialize in recovering and expediting time-sensitive freight. Our technology and services enable us to recover freight from any airport or container freight station across the United States while providing the visibility to see a shipment’s journey every step of the way. Get in touch with Port X Logistics to learn more about how Port X Logistics and Carrier 911 retrieves cargo at breakneck speed.