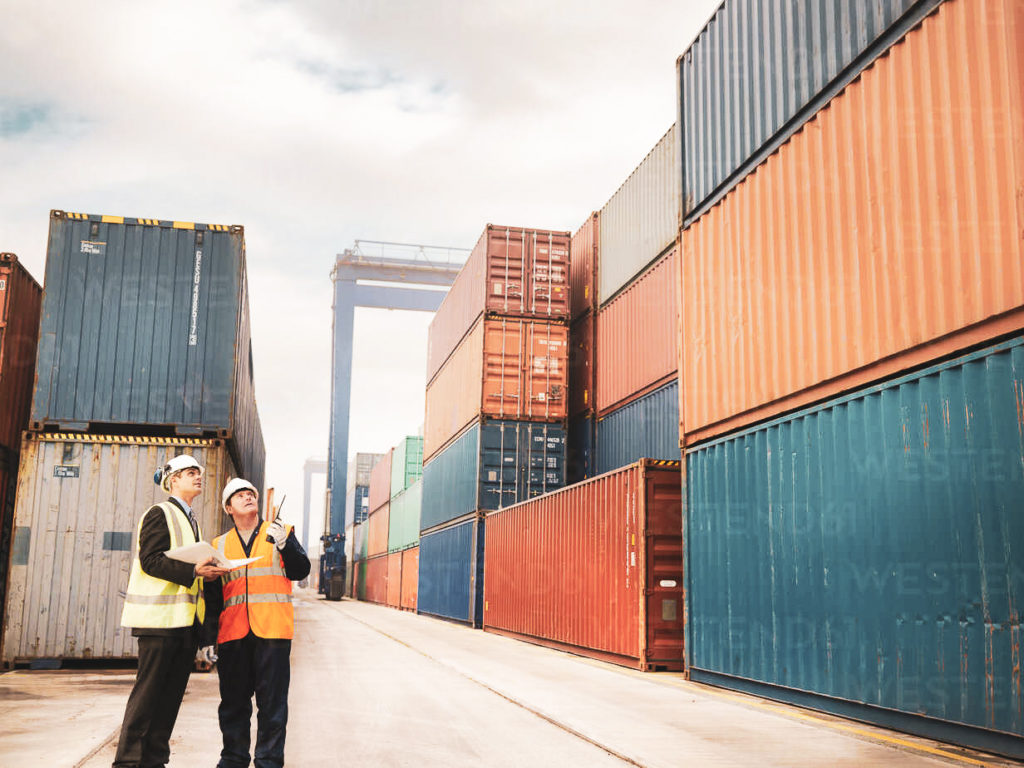
Port X Logistics expert, David Onizuka, got an inside look into the operations of the Port of LA and knowledge about labor shortages, the current volume levels and more.
Can you give me a brief background of what your job is?
I am Senior Vessel Operations Manager with 14 years of experience at one of the mega container terminals in the Port of Los Angeles. In my 14 years, I’ve primarily worked in vessel planning and operations, but do have some experience in all aspects of terminal operations including yard, gate, and rail. As a Senior Vessel Operations Manager, I lead a team of the operations managers who are responsible for the direction of all ILWU labor working vessel ops. There are two key aspects of my job:
1. The coordination of all vessel operations including yard and vessel planning, scheduling and ordering of labor, terminal resource management, vessel/arrival departures, and vessel production management.
2. People management. So much of this job is about building relationships with our managers, labor team, shipping lines reps, etc. A familiar friendly goes a long way here. On any given day we have zero to four vessels working with up to around 300 ILWU workers. A lot of money is spent on ILWU labor every day and we are here to ensure that the ILWU labor we hire are working safely and efficiently.
How do you schedule labor versus ships coming in?
There are several factors to labor availability verse labor demand. It is controlled through a joint effort between the ILWU and the PMA. Each day, the PMA member forecasts their labor needs and the ILWU forecasts their availability. Under normal conditions, there’s usually not any concern meeting the labor needs throughout the LA/LB harbor. However, due to the recent surge in volume the PMA is rationing labor due to not being able to meet the demands of each company.
Currently, the skilled jobs (crane operators and top handler operators) are the hardest jobs to fill. Most of the rationing of labor depends on the availability of these positions.
Priority for labor is given to yard, rail, domestic cargo vessels, passenger vessel and military vessels. All other international vessels are allocated labor based on their arrival time into port. If a berth is not available at their destination terminal, then their arrival is considered to be when they anchor outside the harbor.
Whichever vessel has been in port the longest gets the lowest allocation number (the highest priority for labor). Normally, a mega vessel would have no problem getting labor for up 10 cranes, but under the current rationing each vessel can have no more than enough labor to work four cranes. Each terminal is doing their best at servicing their vessels as fast as possible to clear the backlog of vessels waiting.
Due to the rationing though, even once operations commence, vessels are staying at berth twice as long as normal. This system is not a perfect science as some vessels may be able to reach their berth before others that have been waiting outside at anchor longer.
That may not be fair, but there are some advantages to shipping lines that have relationships at multiple terminals. They can take advantage of their ability to send their vessels to several different berths.
This is not the first time the port has seen labor rationing due to unmeetable demand. In recent years, this has happened in 2014-2015 labor negotiations and subsequent congestion and 2018-2019 tariff increases.
[PMA is the organization that represents the terminal operators and steamship lines in the West Coast Ports. ILWU is the labor union that works in West Coast Ports]
How has COVID affected operations?
We are dealing with all of the normal protocols that the general public is experiencing. Mask wearing, distancing, quarantining if infected or exposed, frequent sanitization of workspaces/equipment, and working from home (although only a small portion of management is able to).
The PMA and ILWU agreed to move the start of the night shift back one hour to allow for more time of sanitizing workspaces/equipment and reduce interactions between day and night shifts. Doing this also eliminates the ability to run a third shift (commonly known as the hoot shift).
However, the biggest effect of COVID on operations has been the disappearance of volume in the Q2 of 2020 and the subsequent surge in Q3 and Q4.
[Per Daily Breeze news article: In December, ILWU members at the Port of Los Angeles saw 65% of its tests come back positive for COVID-19. At the Port of Long Beach, 71% of the reported cases came back positive.
“In just the first seven days of January, 54 more positive cases were confirmed within our ranks,” the local unions’ letter said, calling the situation urgent. “These numbers continue to rise.”]
How has labor shortage affected operations? How has the terminal yard congestion affected operations?
The labor shortage and subsequent rationing has had a huge effect on operations. There’s a massive domino effect across the supply that starts here at the port.
Here’s how it goes.
1. Volume to the west coast surges.
2. Terminal operators begin maxing out vessel operations to quickly service each customer.
3. Terminals quickly get congested due to the surge in imports, exports, and empties.
4. Terminals adjust operating plans to keep up, most commonly putting imports in non deliverable stacks. Most are over 100% of their capacities. Even when imports are available, pickup appointments are often missed due to lack of chassis.
5. Labor availability cannot keep up with demand.
6. Labor rationing begins
7. Terminals can no longer service vessels fast enough due to labor rationing and terminal congestion.
8. Consumer goods are delayed to Americans.
At Port X Logistics, we have you covered. We specialize in expediting containerized cargo with our drayage, trans-load, and trucking services. For more information, visit our LinkedIn page, read our blog, or email us at letsgetrolling@portxlogistics.com